Jolene Baker is a manufacturing intelligence specialist at LSI. She is responsible for the development and administration of OSIsoft PI applications and is an industry expert in the use of Falconry pattern recognition software (an LSI partner). We sat down with Baker to get her take on LSI’s capabilities and learn about her experiences on a past project.
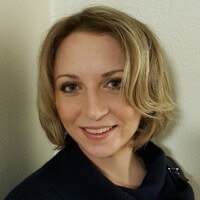
First, give us a little background on LSI.
Baker: We are a global provider of process, mechanical and electrical engineering services and specialize in systems integration, process improvement, automation and information systems. We have a wide range of expertise ranging from PLC at the plant floor to larger scale corporate data needs. Our company values focus on building and maintaining long-standing client relationships.
Tell us about a project where your expertise really made a difference.
Baker: Before my time at LSI, I was part of an interesting project that had us working on maintenance operations in a large soda ash production facility. We used PI software packages and data mining techniques to connect data from multiple sources. Once analytics were in place and the data was readily available, we built applications that supported maintenance planning, production optimization and reporting, plant efficiencies, specialty maintenance tracking on critical equipment, operational forecasting and predictive analytics.
What software applications do you typically use and what applications are they effective for?
Baker: We utilize an Asset Management Database to deposit equipment information, ERP info ( i.e., drawings, specs, etc.), GIS locations, work order information, safety, DCS, Lab, special analysis, machine learning, consumptions, utilizations, runtimes, downtimes and many other applications.
How does that database benefit plant operations?
Baker: The database becomes a single source of the truth that any application can be fed or added too. It is available to all PI users and quickly replaces paper log sheets and reporting methods. This allows real-time data to be compared to the data obtained from operator/foreman logs.
What information do database reports provide in regards to operational forecasting?
Baker: In my soda ash production facility job, turnover reports included a forecasting model that could identify end-of-the-day production rates based on ore feed and pre-and post-filter liquor allocation. The information could be used to identify and flag a process issue for investigation before production was lost for the day.
What predictive analytics solutions did you provide for the soda ash production facility?
Baker: We built analytics for positive displacement pumps that analyzed filtering capabilities to accurately indicate when one of two pistons was under-performing by a given percentage.
How effective were analytics in terms of the identification and notification of performance issues?
Baker: They were extremely effective. The application alerted control board operators on the DCS/HMI within 10 minutes of an underperformance issue being detected. It also sent out a notification to supervisors that included a direct link to a PI web-based data page that allowed both on- and off-site access. Upon receiving the notification, supervisors activated a redundant pump to allow facility operations to continue. This application has already succeeded in helping the plant to avoid significant rebuild costs – twice! Prior to the application initiation, a setback like that would likely have necessitated the complete rebuild of the hydraulic system.
What happened during those instances where analytics saved the facility from costly repairs?
Baker: During the first situation, maintenance was notified immediately when an agitator motor recorded a sudden spike in amps. The spike was a result of a bolt shearing that was used as a support for the motor assembly. The notification allowed maintenance to shut down and repair the agitator before any significant damage took place.
During the second situation, amps from a motor attached to one of two conveyor belts that carried ore from the crusher started behaving erratically. The operations team was not notified in time and the splice for the belt failed due to it rubbing on a stuck section of belt rollers. After this anomaly was captured, it was built into real-time analysis so any future occurrences for belts could be rectified before failure.
After analytics were in place, what applications did you utilize to assist with maintenance planning at the soda ash production facility?
Baker: We monitored amps on crushers and associated bucket elevators in the analytics software to identify when crusher rebuilds were required. This maximized equipment life and performance.
How did you reduce downtime for the customer?
Baker: We reduced clean up and repair time by continuously monitoring bore hole pressures. As a result, appropriate mine staff is now alerted immediately when a significant pressure drop is indicated. These pressure drops are an indication of a blown pipeline in the mine.
Were there any applications used that have notably improved plant efficiency and production?
Baker: There are quite a few, but the most significant would have to be the predictive model that we built using Falkonry software. The model was able to output real-time ore grade using combined data from lab quality, chemical off-gas equation analysis and other plant instrumentation. Identifying ore grade allowed the unit to be adjusted to maximize sensitive process equipment and efficiencies to increase production.
What outcome did your new applications produce in regards to automation and equipment optimization?
Baker: Production and mine reports are now automatically pushed to a new ERP system. This new system identifies mill media charge, using manual data and motor amps for proper charging and equipment optimization. It also provides the opportunity to identify pending flight failure in mill application before it takes place.
How would you describe the overall function of the soda ash production facility’s new analytics capabilities?
Baker: Critical information is now summarized into an on-demand priority report. Power usage, utilization, runtime and downtime are now effectively calculated on all major assets plant wide.
What would you say are the main advantages from working with LSI on projects similar to this or any other project?
Baker: There are many advantages, but efficiency-related cost saving is one of the most important. Because LSI is platform neutral, we are able to help customers maximize their investments by utilizing the best available tools, regardless of who manufactures them.
How are the processes put in place by LSI carried out after projects are completed?
Baker: Our familiarity with the processes and tools allows us to provide customized documentation to all levels of operator and leadership in an organization. We can also provide training so that operation and adjustment of the platform can be handled by our customer’s own employees moving forward.
Does LSI have any experts who specialize in the maintenance field?
Baker: Absolutely! LSI is fortunate to have experienced employees who specialize in projects and preventative maintenance tasks using the Computer Maintenance Management System (CMMS).
Does LSI have any options for customers who are unable to provide internal support upon project completion?
Baker: Yes. LSI has a number of affordable options for ongoing support for new and existing PI systems in the absence of an available internal admin. We can also help with PI support on an as-needed basis.
Are LSI’s services available to smaller facilities as well?
Baker: LSI brings industry expertise that covers large and small applications from the PLCs on the plant floor to the data needs of the corporate office. Our collective knowledge base allows us to excel at connecting all the dots.
Does LSI have any partnerships with well-known manufacturers?
Baker: We maintain respected partnerships with many industrial solution providers such as OSIsoft (PI), Rockwell Automation and Siemens. They are as much a part of our team as we are of theirs.