The Situation
Our dough-tray wash line throughput needs to improve. Whenever we change the sanitization-in-place (SIP) recipe, we need maintenance to adjust the de-stacker VFD for correct conveyor speed. Otherwise, we’ll have downtime due to jams. Can you help us integrate the tray washer and de-stacker controls?
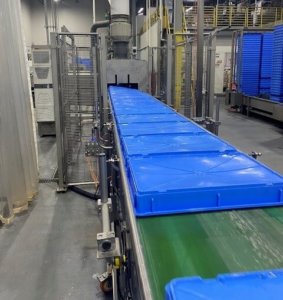
A leading global pizza manufacturer producing pizza crust dough for distribution to their stores was already using automated process equipment in their food manufacturing plant. However, the various pieces of OEM equipment lacked control system integration, they were islands of automation. The tray washing system consisted of three machines that operated independently: a de-palletizer, de-stacker, and tray washer. Depending on the type of dough previously stored in the trays, the SIP recipe also changed in speed and chemical used. The lack of integration between the tray washer and the de-stacker meant frequent tray jams as they were conveyed to the washer. The only way to prevent downtime and inefficient manual operation was for maintenance personnel to access the de-stacker panel. The VFDs were adjusted manually or operators had to feed the trays into the washer manually. Both were time-consuming, inefficient use of resources, and increased safety risks for personnel.
The tray washer OEM offered an integrated de-palletizer/de-stacker; however, the six-figure price tag and the related facilities expense were cost-prohibitive.
The Solution
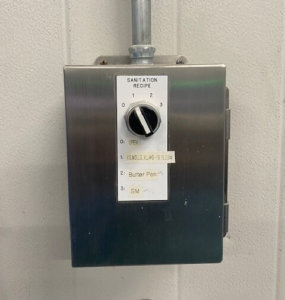
LSI’s team started by visiting the client’s site to evaluate the tray washing process and to fully understand the client’s objectives – LSI Listens. With a clear understanding of the process, LSI provided the control design, hardware, and programming to enable the inclined conveyor to change speed based on the SIP recipe selection. To support the client’s request to easily switch between SIP recipes, a relay panel was designed and installed in a production room near the tray washing line. This relay panel provides the capability to switch between four unique SIP recipes through a simple four-way selector switch.
Because all the SIP recipes are executed in the tray washer, LSI worked with the OEM to determine the best way to integrate the selector switch position to the tray washer settings. The tray washer’s CompactLogix 5380 PLC and the de-stacker’s MicroLogix 1400 PLC programs were modified so that the de-stacker’s VFD speed could be adjusted automatically based on the selector switch position on the relay panel. HMI screens for the de-stacker were also updated to reflect the changes made during the project.
LSI provided:
- Process design and control expertise
- A cost-effective alternative to a capital purchase from the OEM
- System integration of multiple OEM machines
- PLC and HMI programming
- Relay panel design and fabrication
The Results
A consistent, integrated, and reliable tray washing operation.
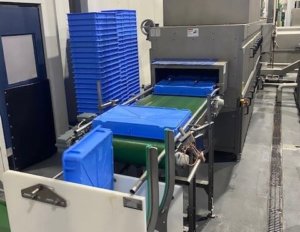
The client no longer needs to involve maintenance personnel when changing SIP recipes. The operator makes the change and counts on the system to work reliably without jams and manual operation. This significantly improves the efficiency and safety of the work environment.
Existing equipment optimized without significant capital spend.
The client was facing a six-figure OEM equipment upgrade to resolve their problems with the tray washing line. LSI resolved the situation with a fully integrated solution, minimal hardware, and no facility changes for less than a tenth of the cost quoted by the OEM.
An expanding relationship.
Due to the project’s success, the client invited LSI to perform an entire plant control system risk assessment. This identified additional opportunities to improve their operation and mitigate the risk of unplanned downtime.
“Andrew was amazing at the upgrade last week. The electric and controls install were flawless, and we had zero production downtime during the week-long project. Thanks for being a great partner.”
~Client Operations Manager
LSI Listened
LSI listened, then our team went to work developing and implementing a solution that seamlessly integrated the de-stacker and tray washer. By focusing on the desired outcome, LSI helped the client optimize their process and reduce their downtime significantly, without a large capital investment.