Our demand for malt continues to grow, our malthouse controls are obsolete and we are experiencing unplanned downtime that affects our throughput and quality. We want to upgrade to ControlLogix with Brewmaxx across all our malthouses, but extended production downtime is not an option. We need an experienced systems integrator to lead this conversion from start to finish, optimize our malting process, clean up our documentation, and develop standards. Can LSI help?
A famous brewing legend once said, “Malt is to beer as grapes are to wine.” So, for one of the world’s largest brewing companies, precisely controlling the malting process is hypercritical to achieving the desired beer flavor profile and appearance. Inconsistent malting and unplanned downtime are unacceptable.
The situation
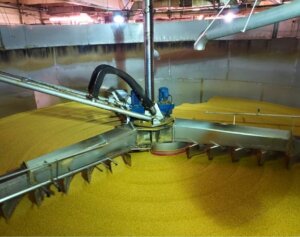
For decades, the client’s iFix /PLC-5 system provided the continuous and batch process control necessary to deliver high-quality malt for brewing at all of their breweries. However, the time had come to upgrade the control system and optimize the process for improved operational performance. As with many old controls systems (this one having been installed well over 20 years ago), the system documentation didn’t match the configuration, and previous changes left a lot of wiring abandoned in place. For this upgrade, the client was implementing Brewmaxx with Rockwell Automation’s ControlLogix control system to replace the existing iFix/PLC-5 controls. This malthouse was the first to implement Brewmaxx from the ground up, so readily available objects and standards did not exist. Development of unique control modules, objects, and control standards, along with the installation of new servers and network infrastructure, was required, adding to the project’s complexity.
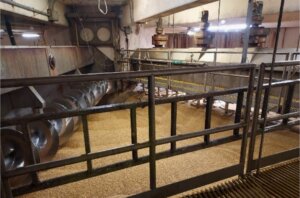
The malthouses located at a single brewery location are mission-critical, as they are responsible for providing malt to all of the client’s North American breweries! Considering the system size, complexity, and downtime constraints, the client requested a multi-phase/multi-year approach for the upgrade, along with assurances of a seamless transition that minimized production downtime. With the implementation of the new system, the client needed to adapt to new troubleshooting and operation methods. To ensure maintenance and operations were ready for the culture shift, a change management project would need to be executed in parallel with the controls upgrade.
The client aimed to mitigate project risks by engaging a single systems integrator that could handle the entire project, with deep domain experience in the brewing and malting industries, as well as expertise in Rockwell Automation and Brewmaxx integration. With expectations running high, LSI was entrusted with leading the project.
The Solution
To mitigate project risks and set the stage for success over the next four years, the LSI/client team embraced two guiding principles: “Walk before you Run” and “Divide and Conquer.” Additionally, LSI worked diligently to get buy-in from all of the client’s stakeholders (including Malting Management, Operations, Maintenance, Electrical Techs, and IT) by co-developing and reviewing the control system standards with the client.
A lot of firsts were experienced by all involved. To get started, the LSI team divided the 8000+ I/O point system into continuous and batch operational areas. LSI focused on the continuous systems (grain handling) in the first year of the project, laying the foundation for addressing the batch recipe-driven areas (steeping, germination, and kilning) in year two. LSI’s expertise in process batch and built-in quality checks made for a smooth SFAT (software factory acceptance testing). Cutovers went as planned due to thorough equipment and signal wiring verification that identified out of service equipment, disabled controls logic, incorrect wire labeling, and defective field devices. These were then flagged ahead of time for removal, repair, and correction to ensure a smooth start-up.
The Results
Consistent, reliable, and efficient malting of the world’s best barley continues, giving the client confidence in their system and ensuring consumers receive the taste, aroma, and color they have come to expect and love in their beer.
- The obsolete control system has been replaced with state-of-the-art hardware and software technology, ensuring the availability of high-quality malted barley is uninterrupted.
- LSI minimized production downtime using around-the-clock/multi-team start-up schedules with construction, production, and the client’s IT department.
- Through the use of LSI’s development system, client Operations and Maintenance personnel received training and became familiar with the new system before the first cutover – setting the stage for a seamless startup.
- The LSI team adapted the client’s existing production scheduling tools to work within the Brewmaxx system, allowing for a seamless process implementation. These changes also streamlined the creation of production batch orders and eliminated many manual data entry points.
What's Next
As a result of the malthouse controls upgrade success, the client is confident in the application of the new technology (Brewmaxx & Rockwell Automation) and LSI’s ability to execute large complex projects. Additional capital projects are already underway, not only in malting but also in other brewing process areas throughout North America.
LSI Listened
After listening to the client’s vision for the future state of controls and automation, LSI worked closely with the client on a comprehensive plan. This plan included building an LSI development system, creating controls standards specific to malting, and implementing 1st order simulation for process verification and training. The development and execution of this project plan delivered transformative changes to the client’s malthouse operations and equipped them with a state-of-the-art robust control system. Most importantly, high-quality malt continues to flow into the breweries of one of the world’s most iconic beverage companies.